How We Make It

So what sets us apart? What has inspired us to be so passionate about taking our craft to the next level? Our team hits the trails: Rock crawling, the dunes, the alpine passes and the slick rock canyons. Not just our team; our friends, family and anyone close to us will tell you that's what we live for. We're building what we wished we had on the trail yesterday. Innovative design based on trail experience. We design it when inspiration hits on the trail... That's what we take to our drawing board.

Above: This Jeep is rocking one of our TJ Flat Belly Skids. While the inspiration for this was the boulder gardens and rock crawling of Southern Arizona, it's been a great addition on the Jeep from the Rubicon Trail to the trails of Moab Utah seen here.
When you buy a product from us, you can be rest assured that we built it like we would have for our own rigs. We don't build it the cheapest and fastest, but it will be the last one you buy due to the material and construction. We stand behind what we make.

Next Venture has been doing business since 2014, however we moved into our current shop location in early 2020. Why the move? We wanted our drawing board and our fabrication shop close to our favorite trails in Western Colorado and Utah. Working and living 90 minutes from Moab, Utah and 2 hours from our favorite Alpine passes provides a lot of opportunities for adventure, good wheeling, and an abundance of new inspiration. You see something different every time you go.
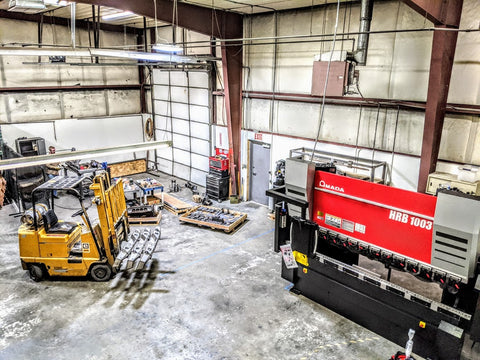
One of our latest additions is an Amada 8-axis CNC Press Brake capable of applying 120 tons of bending pressure, and precision bending with repeatability of 0.004 +/- inches. What does that mean? We're able to form our 1/4" steel brackets and skids precisely for the same correct fitment each time with less welding, less warping, more strength and in less time. It allows us to form anything from a simple bracket to bumpers and complex JL rear corner armor panels. You can check out "Herbie" the HRB model brake in a upcoming blog article.

What we don't do in house, we do with a bit of help from our friends. We've tried on our share of suppliers, vendors and machine shops. Currently, some of our CNC Mill & Lathe work is outsourced. 100% of it is outsourced to local, reputable shops right here in Colorado or just across the border in Utah.
The design work, cnc laser cutting, cnc forming & bending, the hand placed MIG and TIG welds -- we do that in-house right here in Western Colorado -- and we're just getting started.